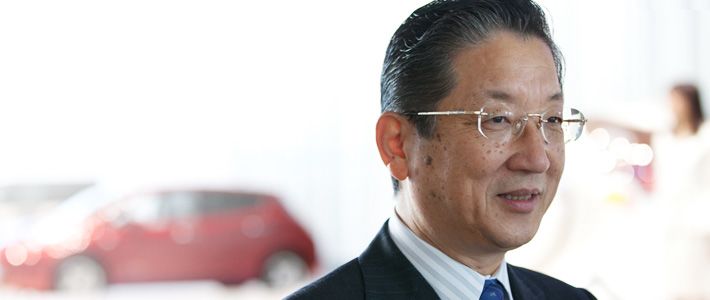
Nissan Motor, una empresa fortalecida en la adversidad
Economía- English
- 日本語
- 简体字
- 繁體字
- Français
- Español
- العربية
- Русский
Lluvia de elogios por la respuesta de Nissan al gran terremoto de 2011
-El gran terremoto con tsunami que golpeó el este de Japón en marzo de 2011 afectó duramente a la industria automotriz y al conjunto de la industria japonesa. La rapidez con que Nissan reaccionó ante el desastre fue valorada y recogida ampliamente por la prensa extranjera. ¿Cuáles fueron las prioridades en su actuación como líder ante un cataclismo como aquel, del que se dice que ocurre solo una vez cada mil años?
Creo que fue muy importante el saber hacer, la experiencia acumulada a través de una serie de hechos previos a ese desastre. A los tres años de ser nombrado director general de operaciones (COO, por sus siglas en inglés), en 2007, ocurrió el terremoto de la coste de Chūetsu, en el que sufrieron graves daños nuestros proveedores de Kashiwazaki, en la prefectura de Niigata, lo cual nos obligó a detener la producción de vehículos. Antes de que esto ocurriera, pensaba que se había hecho todo lo que había que hacer en cuanto a prevención de seísmos, reforzando el edificio y tomando otras medidas antisísmicas, pero las reservas de que disponíamos cuando el proveedor dejó de abastecernos de piezas resultaron insuficientes. Me di cuenta de que, para apoyar a los proveedores y mantener nuestras plantas en funcionamiento después de un desastre así, una premisa fundamental era que desde la central se pudieran dar instrucciones precisas, para lo cual en octubre de 2007 se dio inicio a los ejercicios con simulacro de desastre, llevados a cabo por el Centro de Medidas contra Desastres.
Posteriormente yo mismo me puse al frente del Centro y he venido dirigiendo los simulacros, modificando ligeramente los supuestos cada vez. Los ejercicios que se hicieron el 21 de febrero de 2011, por cierto, fueron los primeros desde que las oficinas centrales se trasladaron a Yokohama. Los estábamos haciendo unas tres semanas antes del 11 de marzo.
En estos ejercicios, se situó en el octavo piso de nuestro edificio central un centro contra desastres ad hoc para ese simulacro. Se colocaron mesas y teléfonos, desde los que se hicieron las comprobaciones iniciales: si los empleados se encontraban bien y si nuestras plantas, las de las compañías relacionadas y las de nuestros proveedores, habían sufrido daños o no. Una vez establecida la magnitud de los daños, estudiamos cuándo estaríamos en condiciones de reiniciar la producción y qué medidas habría que tomar con respecto a los proveedores o a la logística para restablecer esa producción. En los ejercicios dedicamos dos horas, intensivamente, a estas labores.
Cuando ocurrió el desastre a las 2:46 de la tarde del 11 de marzo, yo estaba en el piso 21 del edificio central. Rápidamente di instrucciones para organizar el Centro de Medidas contra Desastres. Unos 30 minutos después bajé al octavo piso por las escaleras y ahí estaban, como en los ejercicios que habíamos hecho tres semanas antes, las mesas alineadas con los teléfonos, así como todo el instrumental para las emergencias, todo perfectamente preparado. Recuerdo que al ver todo aquello pensé en la importancia de prepararse bien para un desastre.
Por otra parte, en el simulacro de febrero se manejó también el supuesto de que hubiera que dar cobijo a las personas, empleados o no, que previsiblemente tendrían dificultades para regresar a sus casas. Esto también fue muy positivo. El día del desastre consideramos que sería necesario ofrecer alimentos tanto a los empleados como a otras personas en esa situación y, cociendo todo el arroz que teníamos en la empresa, hicimos 1.800 onigiri (bolas de arroz cocido). Teníamos también más de 2.000 mantas, que fueron útiles para muchas personas.
-¿Quiere decir que estar preparado es lo que permite formarse un juicio acertado?
Efectivamente. Yo creo que es importantísimo preparse suficientemente para el desastre, hacer los simulacros, y ser capaz de reaccionar rápidamente en esos primeros momentos de la emergencia. El fruto de estos ejercicios continuos se vio no solo en el caso del edificio central, sino en el de las plantas de Tochigi e Iwaki, que sufrieron los efectos del terremoto. En las fábricas de las zonas afectadas hubo sitios donde se desprendió del techo la cinta transportadora de la línea de producción, o se derrumbó el cubilote (horno vertical) de una fundición. Y sin embargo no resultó herida ni una sola persona. Es la mejor plasmación de lo que significa el ejercicio constante.
Oí lo que contaba la gente después de aquello, y parece que la clave estuvo en que habían repetido una y otra vez los ejercicios de evacuación y lo tenían todo aprendido con el cuerpo más que con la cabeza. Por ejemplo, en una planta de fundición el aluminio fundido estaba a punto de verterse al suelo, y si los empleados hubieran escapado sin preocuparse de nada más, podía haber ocurrido un incendio. Pero no, se pusieron a salvo después de haber colocado la tapa que evitaba que se vertiera. Yo me emocioné mucho al saber que en medio de temblores como aquellos habían sabido obrar con tanto cuidado.
La experiencia de la revitalización de Nissan fue útil ante la crisis
-Tengo entendido que Moody’s elevó en julio de 2011 la calificación de Nissan precisamente en razón de esa gestión de riesgos a la que usted se refiere. ¿Podría explicarnos una vez más por qué Nissan tiene esa elevadísima capacidad de respuesta ante los desastres?
Creo que en esa primera reacción, como acabo de decir, es crucial el entrenamiento continuo. En el posterior proceso de reconstrucción creo que fueron muy efectivos los métodos gerenciales introducidos a raíz del Plan de Revitalización de Nissan (Nissan Revival Plan) iniciado en 1999 con el nombramiento como director general de operaciones de Carlos Ghosn.
Por lo general, cuando las fábricas sufren daños es el Departamento de Producción el que hace frente a la situación, y cuando son los proveedores los afectados, lo hace el Departamento de Compras, es decir, que lo más habitual es seguir un esquema vertical, pero en Nissan Motor tenemos el llamado Equipo de Funciones Transversales (Crossfunctional Team), un esquema más horizontal, que permite llevar a cabo ciertas labores reuniendo personal de diversos departamentos. En cada departamento suele haber una mentalidad propia, forjada a través de los años, que contribuye a ese esquema vertical que tanto daño produce. Pero cuando los diversos departamentos actúan según este esquema de funciones cruzadas, se consiguen ideas novedosas.
En nuestra empresa tenemos un código, el “Nissan Way”, que fija las directrices para el comportamiento de cada empleado, y en cuyo primer artículo se recoge, precisamente, esta funcionalidad cruzada o transversal, una idea de diversidad en el sentido de aceptar opiniones y pensamientos diferentes a los propios.
Como ejemplo concreto pondría lo que ocurrió cuando, después del desastre, se nos comunicó que las instalaciones de algunos proveedores habían sido destruidas por el seísmo y que eran incapaces de seguir fabricando piezas. Personal procedente no sólo del departamento de Compras, sino también de los de Producción y Mantenimiento acudió rapidamente para ayudar en su restablecimiento. Cuando había que abastecerse de piezas alternativas en otra compañía, enseguida el departamento de Desarrollo sometía esas piezas a las pruebas de rigor. Si no era posible dotar al vehículo con sistema de navegación por haberse sufrido retrasos en piezas con circuitos integrados, el departamento de Ventas no tardaba en dar a los clientes las explicaciones necesarias. Ya no era aquello de “¡no hay piezas!”, “¡a ver, los de Compras, que se muevan!”, porque se había conseguido un ambiente en el que todos unían sus fuerzas.
Me sorprendió muy positivamente, en especial, el hecho de que en el departamento de Desarrollo, que de ordinario funciona con un único turno, se establecieran turnos de día y de noche para realizar las pruebas de calidad de las nuevas piezas alternativas. Supongo que aquella fue la primera vez que se hizo en Nissan turno de noche en el departamento de Desarrollo. Gracias a ellos, se pudo comprobar que las piezas alternativas eran válidas y pasamos a producir en serie con un retraso mínimo.
Esa cultura de la funcionalidad cruzada que veníamos promoviendo en Nissan como parte del proceso de revitalización dio sus frutos en aquella situación de emergencia.
Me gustaría destacar también la efectividad de nuestra “interregionalidad”. Ocurrió que en las plantas en el extranjero la producción quedó paralizada al haber sufrido algunas fábricas japonesas los efectos del terremoto y retrasarse la producción de piezas. Pero en nuestro caso el descenso en la producción registrado en las plantas en el extranjero fue realmente muy pequeño.
Tras el terremoto, muy pronto, los responsables de las fábricas de Nissan en América, Europa, China, Tailandia, Indonesia, etcétera, se reunieron en el muelle de Honmoku (puerto de Yokohama, en la prefectura de Kanagawa), que es el centro de nuestra logística. Llegaron a ser cien personas, de las más variadas nacionalidades. Partiendo de la situación de la producción en sus países, y viendo cómo iba restaurándose la capacidad de producción de piezas en Japón, establecieron conjuntamente la forma más efectiva de distribuir las piezas. No se disputaron las escasas piezas disponibles, sino que, gracias a un trabajo de equipo que iba más allá de los límites regionales y que partía de una perspectiva global, se las apañaron para no causar un bajón en la producción. Esa “diversidad” es también uno de los pilares del código “Nissan Way”, pero aún así fue muy emocionante comprobar que estábamos consiguiendo estas cosas de una forma enteramente natural.
Superación de la crisis empresarial
-¿Qué dificultades tuvieron que afrontar hasta que esa cultura tan efectiva ante las crisis arraigó en la empresa?
Creo que es importante el hecho de que en los años noventa Nissan atravesara una crisis gerencial. A partir de 1999, cuando se estableció la alianza con Renault, las finanzas de la empresa fueron evolucionando favorablemente, pero en 2008 volvimos a una situación de peligro con motivo de la crisis financiera internacional. De modo que en nuestro personal ha calado hondo la idea de que para superar una crisis hay que enfrentarse a ella con medidas intensivas.
Con la crisis de los noventa, estuvimos en números rojos durante ocho años. Esta situación se eternizaba y la gente acabó acostumbrándose a que los resultados empresariales nunca mejoraran. Si se tomaban medidas eran siempre a la zaga de los acontecimientos y cuando se trataba de complementarlas con otras, ya era demasiado tarde y las cosas no hacían sino empeorar. Actuando siempre tarde, a toro pasado, no había manera de salir a flote. Con el Plan de Revitalización de Nissan, que hicimos público en 1999, aprendimos por fin que para recobrarse lo antes posible hay que enfrentarse a la crisis con medidas intensivas, aunque puedan ser un tanto dolorosas.
Con este último terremoto, hemos vuelto a concentrar todas nuestras fuerzas en las medidas. Detuvimos durante tres meses todos los trabajos de Desarrollo y dejamos de hacer horas extras en todas las secciones de la empresa. Cerramos el grifo de casi todos los gastos, reservando la liquidez en previsión de un deterioro de la situación. Creo que resultó fácil transmitir el mensaje a los empleados, tratándose de medidas instantáneas e intensivas. No se trataba, pues, de responder al desastre dejando de producir en atención a la situación del país, sino de una decisión empresarial fundamentada. Yo creo que los empleados lo entendieron perfectamente como una forma de gestión de riesgos, y colaboraron en todo momento.
El precedente de la actual gestión de riesgos se remonta más o menos al año 2001, cuando ya habíamos puesto manos a la obra en el Plan de Revitalización de Nissan. Después vino un proceso de ensayo y error, en el que fuimos identificando los factores de riesgo que afectaban a la continuidad de la empresa, se elaboró un mapa de riesgos, a cada riesgo se le asignó un directivo como responsable de riesgo que se encargaría de tomar las medidas oportunas. Conforme se ejecutaban las medidas y esos factores iban borrándose de la lista, se identificaban nuevos factores y se iban ejecutando nuevas medidas, que es lo que se llama “ciclo PDCA” (iniciales en inglés de plan, do, check y act). Entre ellas estaban las medidas en caso de terremoto, y los BCP (plan de continuidad del negocio, por sus siglas en inglés) para los proveedores.
Que la gestión de riesgos funcione ante una emergencia hace posible también afrontar grandes retos como empresa. Nissan ha adoptado un método que le permite no estar a la zaga de otras empresas a la hora de establecer, por ejemplo, una estrategia para los países emergentes, o para afrontar el asunto de los vehículos eléctricos, es decir, crear una estrategia propia y original e ir obteniendo resultados en el camino hacia esos objetivos. Cuando se va a la zaga de otros, se puede actuar viendo sus fracasos y correr pocos riesgos. En cambio, si Nissan trata de hacer algo tomando la delantera al resto, eso implica muchos riesgos. Cuanto más atrevida sea esa estrategia de asumir riesgos, tanto más necesaria se hace una gestión de riesgos que contemple todas las posibilidades.
No es posible el crecimiento cuando solo ves el peligro inminente, cuando, por ejemplo, te abstienes de invertir preocupado por riesgos como el fin de la burbuja china o la crisis del euro. Me da la sensación de que hoy en día la economía japonesa ha caído en eso. Aun en este contexto, Nissan ha adoptado una estrategia decidida y está tomando la iniciativa aquí y allá. Nissan Power 88, el plan empresarial de medio plazo que hizo público en junio de 2011, está lleno de audacia y ambición.
La gestión de riesgos consiste en una preparación permanente ante fenómenos como una gran catástrofe o una crisis económica de escala mundial, pero al mismo tiempo es una preparación para crear una visión y una estrategia audaces e ir avanzando hacia los objetivos. Yo creo que tiene esos dos significados.
Los automóviles sostienen la industria japonesa
-Nissan siempre un paso por delante y el gobierno, me parece, siempre un paso por detrás. Por lo que respecta a las medidas de ahorro de electricidad y otros asuntos, daba la impresión de que ustedes llevaban el liderazgo.
En la industria automotriz pensamos que somos una de las industrias punteras de Japón, que estamos sosteniendo la industria japonesa. Abordamos los problemas convencidos de que si nosotros no lo damos todo, Japón lo va a pasar mal.
Si vamos a las cifras, vemos que en 2010 la exportación de automóviles y piezas supuso un total cercano a los doce billones de yenes. La importación se situó en torno a los 600.000 millones. Solo con los automóviles contribuimos al superávit comercial con once billones de yenes. En el total de la balanza comercial de Japón la exportación supuso 67 billones de yenes y la importación 61 billones, con un superávit de seis billones, de forma que si la industria automotriz deja de exportar pasaremos a tener déficit comercial. Y eso fue exactamente lo que sucedió en abril de 2011, cuando nuestra industria se vio obligada a detener la producción debido al terremoto: se llegó a un déficit comercial. Un déficit de la balanza comercial se refleja tarde o temprano en la balanza por cuenta corriente y en la emisión de deuda pública. La responsabilidad con que carga la industria automotriz es enorme.
Por desgracia, en Nissan nos vimos obligados a detener la producción después del terremoto y de ello se derivaron grandes consecuencias para la economía japonesa. En las zonas afectadas teníamos cerca de 500 proveedores, que representan una importante fuente de empleo. Si la industria automotriz no reinicia su producción, todas estas fábricas no pueden volver a funcionar. Los materiales químicos del complejo petroquímico de Kashima, así como la siderurgia, tampoco se mueven si no nos movemos nosotros. Teníamos que cumplir con nuestra misión: levantarnos cuanto antes y volver a tirar del carro de la economía japonesa. Teníamos una fuerte conciencia al respecto.
Con los cortes de electricidad que se establecieron para paliar la insuficiencia de electricidad tuvimos que detener la producción, lo cual fue un jarro de agua fría sobre nuestro entusiasmo. Inicialmente, se planeaba aumentar la producción poco a poco a partir de julio y entrar de lleno en fase de incremento entre el verano y el otoño. Nuestra intención era causar un impacto positivo tanto en las zonas afectadas por el terremoto como en el conjunto de la economía, contribuir a la recuperación de Japón, pero nos vimos frenados por estos cortes.
Pero tampoco podíamos ser nosotros la causa de mayores cortes eléctricos. La industria del automóvil utiliza una gran cantidad de energía eléctrica. Se dice que los jueves y los viernes son los días de mayor consumo, así que si parábamos esos días el pico de consumo se moderaría hasta los niveles normales y el resto de los sectores industriales podrían trabajar con normalidad, así que en el conjunto del sector automotor nos decidimos a trasladar a esos días los descansos semanales.
Nos parecía que esta medida era la mejor forma de contribuir a la sociedad y así lo hicimos, pero lo que más me alegró fue oír decir, tanto a los empleados y sus familias, que estaban sufriendo esa incomodidad en sus vidas, como a otras muchas personas de las áreas circundantes que también habían sufrido molestias, que “lo habían pasado mal, pero que había sido para contribuir a la sociedad”. En tanto sirvió para que cada uno de los empleados sintiera la gran responsabilidad social de la industria automotriz, creo que mereció la pena hacerlo, aunque fuera duro para los empleados.
Hacia la nueva crisis causada por el alza del yen
-Con la llegada del invierno es posible que haya nuevos problemas de abastecimiento de energía. Pero es que, además, con el alza del yen y el encarecimiento de los combustibles la industria manufacturera japonesa esta sufriendo una durísima prueba. ¿Cómo se disponen ustedes a afrontar esta crisis?
Lo más duro es, sin duda, el alza del yen. Cuando un país va fortaleciéndose y comienza a sentirse la riqueza, es lógico que vayan subiendo los salarios y que su divisa también se aprecie. Con una moneda cara, las empresas con un valor añadido comparativamente menor y un uso intensivo de la mano de obra dejan de ser rentables y se van al extranjero. De esta forma países que eran pobres van haciéndose ricos. Por contra, los países que se han enriquecido comienzan a importar demasiado y pasan a tener déficit en la balanza comercial, con lo que se deprecia su moneda. Con esa depreciación el país recupera su competitividad y otra vez es capaz de exportar. Yo siempre sostengo que la macroeconomía se fundamenta en esta estructura.
Nadie podrá negar que, junto con este ciclo, se produce una renovación industrial, que va hacia productos con un mayor valor añadido, y que no hay necesidad de proteger aquellas industrias que van perdiendo su competitividad. Otra cosa muy distinta es la protección de las industrias tradicionales. Si una industria pierde su competitividad, según las leyes del mercado, tiene que dejar sitio a otras. Y además hay que ocuparse de crear otra industria que sustituya a esa como eje de la economía. Es un principio lógico.
Por regla general, esta renovación de las industrias supone un cambio gradual desde las menos competitivas hacia las que lo son en mayor medida. Mientras una va sustituyendo a la otra, va elevando su productividad y su nivel tecnológico. Sin embargo, la abrupta alza del yen que sufrimos actualmente está saltándose ese proceso de renovación y tiene una fuerza destructiva que podría dar al traste con la competitividad de cualquiera. De los aproximadamente 120 millones de japoneses, la población empleada es de 54,79 millones. La industria manufacturera emplea a una quinta parte, es decir, a unos 10,36 millones de personas. Uno se pregunta quién dará empleo a esos diez millones de personas cuando desaparezcan las manufacturas.
Se oye decir a veces que si el yen está alto las manufacturas pueden trasladarse al extranjero, y que sectores como la agricultura, la salud pública, la atención a ancianos y enfermos, o a los niños de preescolar podrán emplear a esas personas. Pero no parece que esos 10,36 millones de personas puedan encontrar trabajo en los campos, hospitales, residencias o guarderías. Hará falta una nueva industria que sirva de eje al desarrollo. Es posible que esa industria sea la industria medioambiental, o la informática. Pero actualmente la industria que lo sostiene todo es la automotriz. Trasladarnos al extranjero antes de haber encontrado a quien nos tome el relevo sería una irresponsabilidd en la que nuestra industria no va a incurrir.
Si, como responsable de una compañía, me dicen que siga haciendo negocios aunque el yen se cotice a 50 unidades por dólar, podría hacerlo. Lo que ocurriría es que, aunque Nissan Motor lograra sobrevivir, Nissan Motor de Japón desaparecería. Y yo creo que no puede permitirse que ocurra una cosa así.
Me preocupa mucho que hoy en día no exista una conciencia compartida sobre el hecho de que estamos ante una crisis de esas proporciones. Si esta alza del yen se prolonga cinco años, en Japón la deslocalización industrial será total. Cuando deje de ser viable la industria manufacturera, ¿cómo vamos a sostener un país como Japón? Esto me sigue preocupando mucho.
-Escuchándole, se percibe que la industria automotriz es como un espejo en el que se puede ver reflejado todo Japón. Recogiendo también esa reflexión, ¿podría decirnos, para finalizar, en qué consiste el atractivo de los coches japoneses?
Pues, sin duda, ese espíritu de hospitalidad, de agasajo, que es tan propiamente japonés, y que se dirige también hacia la persona que se va a sentar en el vehículo. Esa sensación de placer, de felicidad, que envuelve a la persona que se mete en el coche. Ese es el coche que queremos hacer llegar al cliente, ese es el espíritu con el que lo fabricamos.
Ofrecemos además el placer de la conducción. Y otras muchas cosas, como la atención que prestamos al medio ambiente, pues se han anulado los gases de escape, o al menos se han conseguido gases con bajísima proporción de dióxido de carbono. Y un alto nivel de seguridad. Estas cosas se han convertido en requisitos para los coches japoneses. Y no hay que olvidar la gran atención que se presa a la calidad del producto, y que es un rasgo tan japonés.
Agasajo, placer de conducir, consideración hacia el medio ambiente, seguridad y la calidad del producto. Tales serían los cinco atractivos del vehículo japonés.
Entrevistador: Harano Jōji, director de la Fundación Japan Echo.
Fotografía: Kawamoto Seiya.
(Traducido directamente del japonés)
Gran Terremoto del Este de Japón desastre crisis financiera restauracion Nissan balanza comercial seguridad energetica alza del yen