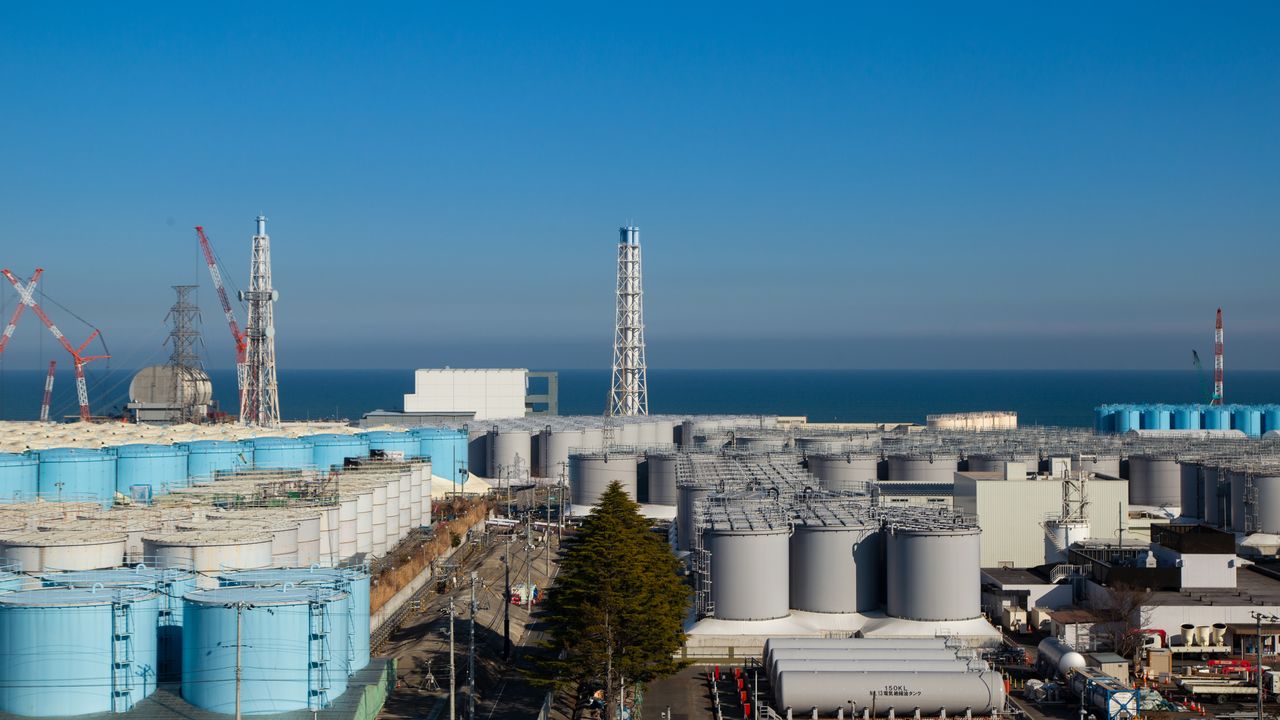
Fukushima Daiichi: Progress to Date and the Challenges that Remain
Society- English
- 日本語
- 简体字
- 繁體字
- Français
- Español
- العربية
- Русский
The triple disaster set in motion on March 11, 2011, unfolded like a three-act play, with the raising of each curtain revealing new and awful horrors. I was working on the tenth floor of a Tokyo office building when the Great East Japan Earthquake struck at 2:46 in the afternoon, paralyzing me with such fear that I forgot to take even rudimentary safety measures. My alarm at the quaking was soon superseded by sinking dread at seeing the television stations broadcast scene after scene of massive tsunami waves swallowing coastal communities whole and, over the following days, hydrogen explosions rocking the reactor buildings at the Fukushima Daiichi Nuclear Station.
While the physical scars of 3/11 have gradually faded over the last nine years, the destruction at Fukushima Daiichi has made a lasting impression on me for being the result of human behavior. Japan watched from afar as the 1986 Chernobyl disaster unfolded, and the accident enlivened the Japanese anti-nuclear-power movement. However, fear and popular outrage subsided, giving way to the demands of the electronics age. Japan needed nuclear power, and consumers bought into the “safety myth” touted by the government and the industry. I was certainly no different. While aware that a meltdown was a possibility, I pushed aside any niggling concerns by convincing myself that the serious-minded engineers in charge of plants would take every precaution to prevent an accident. Fukushima shattered this sense of security. I still remember numbly watching time and again as the Daiichi reactor buildings exploded, unable to believe what I was seeing.
Steam billows from the mangled remains of the Unit 3 (left) and Unit 4 buildings at Fukushima Daiichi on March 15, 2011, following hydrogen explosions. (Photo courtesy Tokyo Electric Power Company Holdings)
On-Site Radiation Low
In February of this year, I visited Fukushima Daiichi to see first-hand how cleanup operations at the plant are progressing. After completing the initial registration process, I was shown into a room where I was given items to wear for the tour. Until a few years ago, journalists visiting the site had to wear a protective suit and mask that covered the entire face. Workers have made progress in decontaminating the site, including removing debris scattered when the reactor buildings exploded, so that now radiation levels are low enough that special protective attire is required in only a few hotspots. To my surprise, my costume consisted of a vest made from nonwoven material, cotton gloves, socks, a mask to protect against dust, a helmet, and a pair of rubber shoes for walking around the grounds.
A display at the TEPCO Decommissioning Archive Center in Futaba, Fukushima, shows the different types of suits worn by workers at Fukushima Daiichi.
Carts full of masks await workers. The type of work to be conducted and site location determines what mask is to be worn.
Before heading out on the tour, I place my visitor’s ID and a dosimeter into the pockets of my vest, facing outward, as instructed by the TEPCO guide. The vest provides no protection from radiation but is a safety measure making it easy to distinguish me as a guest and not a trespasser. Slipping on the other items, I headed outside, noting a sign requesting that people remove their shoes at a designated area upon returning to prevent from accidentally tracking in radioactive contaminants.
Cotton gloves and socks are part of the attire provided to visitors. Participants are asked to tuck in their pant legs during the tour to keep dust and other particles from getting in.
Visitors during a tour wear helmets, vests, and dust masks.
The tour starts with a short drive up an embankment overlooking the plant’s reactors. As the car draws nearer, the steel frame of the reactor 1 building, stripped bare by a hydrogen explosion, comes into view. At around 100 meters away, we stop and I step into the open air, both amazed and a little wary at how close we are to the crippled reactors. Debris remaining on the roof of the number 1 reactor building continues to emit radiation, and the dosimeter shows a level of 118 microsieverts per hour. At that amount, the guide assures us, it would take 10 hours of exposure to reach one millisievert, the average amount of ambient radiation a person absorbs in one year. Nonetheless, we stay for only a few minutes before heading to the next stop.
The heavily damaged Unit 1 building is the only structure housing a reactor at Fukushima Daiichi that is still uncovered.
As we drive, the dosimeter in my vest pocket begins beeping, signaling that I have absorbed 20 millisieverts of radiation. Four more alarms would mean I had reached 100 millisieverts—an amount equivelant to flying from Tokyo to New York—which is the limit permitted before the tour is stopped. The warning leaves me feeling a little uneasy, and I wonder how the workers we pass along our route deal with the concerns of laboring at the site of a major nuclear accident.
A dosimeter reads 118 microsieverts per hour in an area near the damaged reactor buildings. Although cleanup efforts have lowered radiation levels, the contaminated debris that remains is still a concern for workers.
Cranes and other equipment around the Unit 1 (left) and Unit 2 reactor buildings.
Melted Fuel Still Hot
Exiting the car, I find myself gazing up at the reactor buildings. Workers have erected scaffolding and walkways around the structures, which together with equipment like towering cranes gives the area the appearance of a construction site. A closer look, however, reveals twisted steel frameworks and shattered walls that provide a stark reminder of the destructive forces unleashed after the plant’s cooling systems failed and the reactors in Units 1, 2, and 3 underwent meltdowns. Contemplating the scene, I realize that before the accident, few people gave any thought to Fukushima Daiichi, which sits more than 200 kilometers north-northeast of Tokyo. It remained out of sight and out of mind for metropolitan residents like me, who hungrily consumed electricity from the plant without concern for the raw power harnessed to generate it.
A dome-shaped cover installed atop the Unit 3 reactor building helps contain radiation.
Naked steelwork visible through a gap in the outer wall of a reactor building.
A major obstacle in decommissioning the plant is removing melted fuel at the bottom of reactors 1–3. In January 2018, TEPCO confirmed deposits of fuel debris on the floor of the containment vessel of the number 2 reactor, and in February of the following year a robot equipped with pincers succeeded in grasping a piece of the debris. Encouraged by the success, the government updated its roadmap for decommissioning the plant, readying to begin fuel debris removal inside the reactor on a trial basis in 2021. However, there have already been delays, and it remains to be seen whether work will progress on schedule.
A crane and other equipment for dismantling an exhaust stack stand next to the Unit 2 building.
An onsite dosimeter displays radiation levels.
TEPCO also has to figure out what to do about the vast amount of contaminated water leaking into the reactors. Along with water for cooling the melted fuel, rain and groundwater seep in, producing hundreds of tons of tainted water that must be pumped out, decontaminated, and stored in tanks. To reduce the inflow, the utility in 2018 installed equipment that created an “ice wall” of frozen soil around Units 1–4.
A gray scaffoldlike structure around the Unit 4 building was built to support equipment for extracting fuel rods. Offline on March 11, it was the only reactor among Units 1–4, located in the main plant area, that did not melt down and has since had its fuel successfully removed.
Pipes carry coolant chilled to –30ºC to the “ice wall.” The perimeter of frozen soil helps divert groundwater flowing toward the sea away from the reactors.
Treated Water a Growing Dilemma
The contaminated water contains radioactive substances including high concentrations of cesium and strontium. TEPCO treats the water using seven multinuclide removal equipment (ALPS) systems that remove enough of the radionuclides to bring the radioactive contents to safe levels. However, the ALPS systems are unable to filter out tritium, a substance that—although considered to be of low toxicity—has impeded TEPCO’s ability to dispose of the treated water.
A building housing ALPS systems for treating water contaminated with radioactive material.
Equipment to process accumulated water. The ALPS systems are able to remove most radioactive contaminants.
The issue for the utility is not regulatory, as tritium within given limits may be discharged into the environment, but ethical. The nuclear disaster devastated Fukushima’s agriculture and fishing industries. Although production has made a gradual comeback, farmers and fisheries still grapple with the lingering stigma attached to the word Fukushima. National and local authorities have gone to great lengths to promote the safety of products from the prefecture, and TEPCO has been reluctant to release tainted water into the environment, even at levels below international standards, due to the impact it would have on the marketability of the region’s products.
However, the company is quickly running out of options. TEPCO already stores 1.18 million tons of treated water in some 1,000 steel tanks at the Daiichi site, and more containers continuously need to be built. Measures like the ice wall have succeeded in reducing the amount of contaminated water needing to be treated, but at current rates the utility expects it will run out of land for building new tanks by 2022. Planning for this eventuality, the Ministry of Economy, Trade, and Industry in January 2020 proposed disposing of treated water by releasing it into the Pacific Ocean or evaporating it into the air. Whether the government opts for one or both approaches, it faces an uphill struggle to convince local authorities, who want to avoid further damage to the local economy, that this is the best solution.
After two hours touring the site, I returned to the front office building. My dosimeter, which thankfully had remained silent following the first alarm, read 30 microsieverts, about the same amount of radiation as a single chest x-ray. Although I felt some relief at this, what I saw on the tour brought home the fact that the Fukushima Daiichi disaster is far from over. Residents have slowly returned to their homes and the prefecture’s economy is gradually improving. However, decommissioning work is inching along and the prospect of removing melted fuel debris is still far off. As long as contaminated water continues to accumulate, TEPCO will need to find a way to dispose of it, again putting local communities under a cloud of nuclear contamination.
A row of steel tanks for storing treated water.
The site is already crowded with tanks, and space for constructing additional vessels is quickly running out.
The Fukushima Daiichi disaster forced Japanese to confront their consumer habits. Like most people, I jumped on the conservation bandwagon as nuclear power plants went offline and rolling blackouts gripped areas of the country. However, once utilities switched to alternative energy sources to make up for the loss of nuclear and supply recovered, my skepticism of the nuclear industry gave way to other concerns. Just as I had been lulled by a false sense of safety before the meltdown, I fell into my old ways and blindly accepted that TEPCO and the government had the cleanup operation well in hand.
The issue of disposing of treated water illustrates just how precarious the situation is, though. Fukushima’s agriculture and fishing industries have fought hard to win back the trust of consumers by setting safety standards for products far more stringent than global averages. But all this could be undone by the government’s plan to release treated water into the environment. TEPCO faces huge technical issues in mothballing the plant for good, but it is the ongoing impact on the lives of people in Fukushima that is the most salient relic of the disaster.
Equipment for cutting up an exhaust stack.
A bus serves as a control room for workers guiding equipment by remote control in areas where radiation remains high. The pictures on the side of the vehicle were drawn by the children of employees who work onsite.
(Originally published in Japanese. All photos by Hashino Yukinori of Nippon.com unless otherwise noted. Banner photo: Tanks filled with tritium-contaminated water surround the Fukushima Daiichi site; the Unit 3 structure, with its dome-shaped covering, is visible at left.)
TEPCO Great East Japan Earthquake nuclear power Fukushima Daiichi